Can the handwoven warp and weft survive technological modernity?
By Anne Petry, India
Is there any other country in the world as colorful as India? Indian clothing is a visual explosion of vibrant and bright colors. I am always amazed by the tremendous variety of textiles and huge diversity of traditional outfits. All this is possible thanks to the knowledge of weaving mastered by millions of Indians for centuries. Let’s take a historical and geographical journey through India to discover the nation’s weaving arts.
Ancient Knowledge
Silk saris are the quintessence of traditional women’s clothing in India. The nicest saris often go from generation to generation as a family heritage. In the same way, secrets of weaving and the art of decorating silk and cotton are transmitted from masters to students. This helps explain why weaving became an intrinsic symbol of Indian culture.
In Indian history and Hindu myths, a few points can be highlighted. In ancient Veda texts several references are made to hiranya (cloth made out of gold), and in sacred literature it is said that the traditional sari from Madhya Pradesh was brought by Shishupal, Krishna’s cousin. The first evidence of weaving in the country dates back to the Indus Valley Civilization, which was active from 3300 to 1300 bce. The first weaving centers appeared in the 12th and 13th centuries to provide saris for royalty. Thus, the art of weaving is fully part of Indian history and is deeply engraved in Indian life and culture.
In this vast and diverse country, one can find as many clothing habits and traditional weaving techniques as indigenous populations. While shimmering colors remain a common point to all Indian fabrics, each region has its own designs, characteristics, embroideries, patterns, printing techniques and dyeing. Traveling from one state to another means discovering not only new customs but new textiles. Let’s explore some of them.


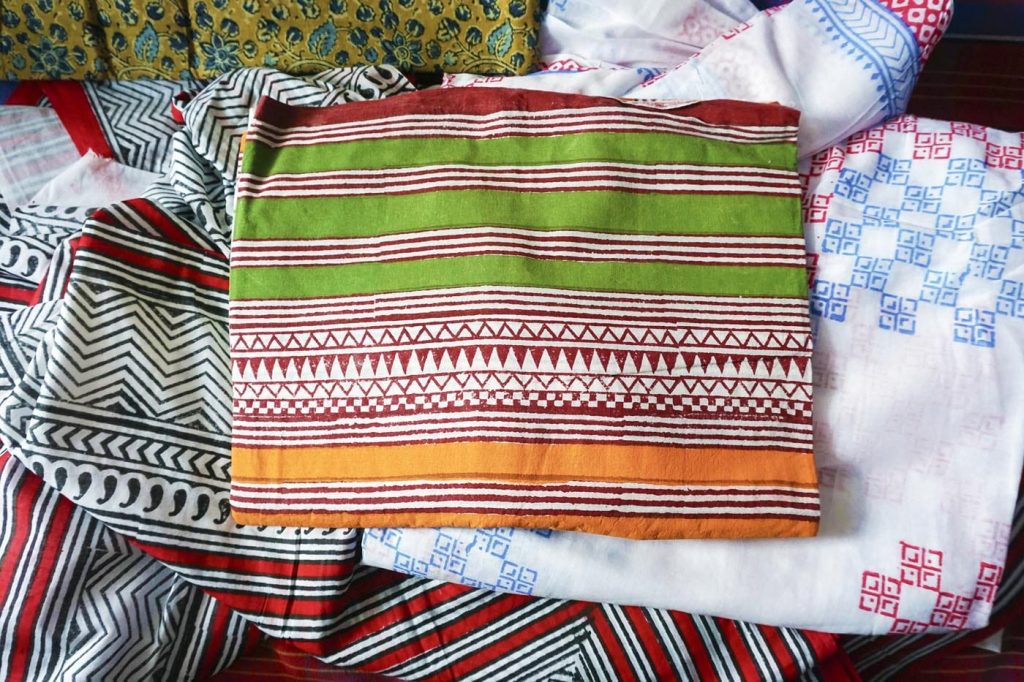
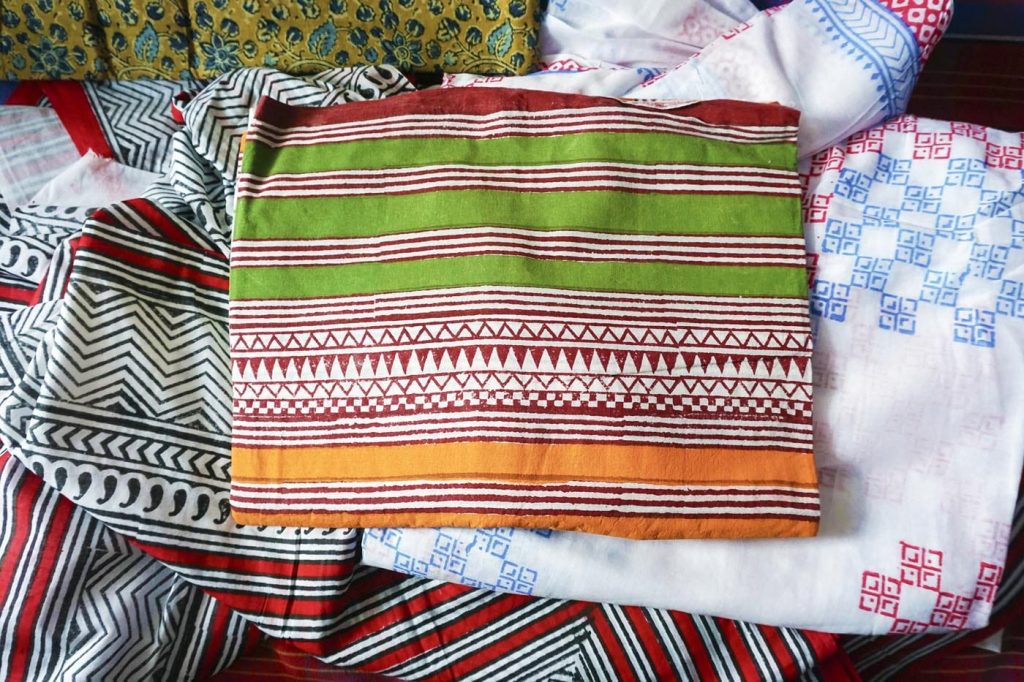
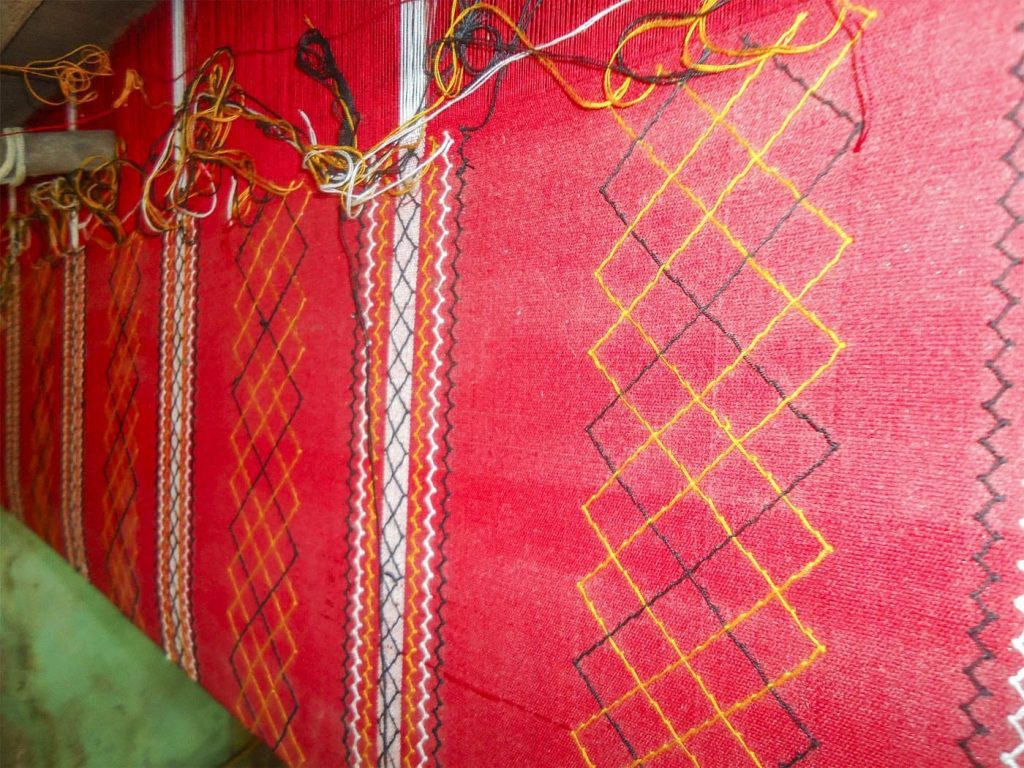
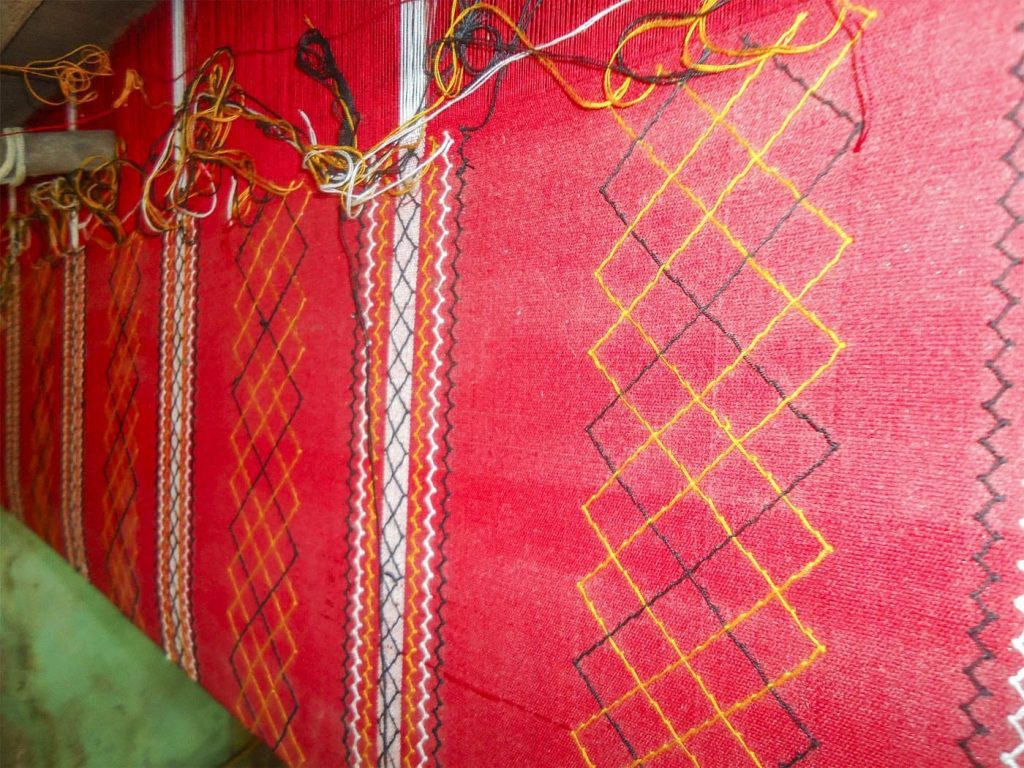
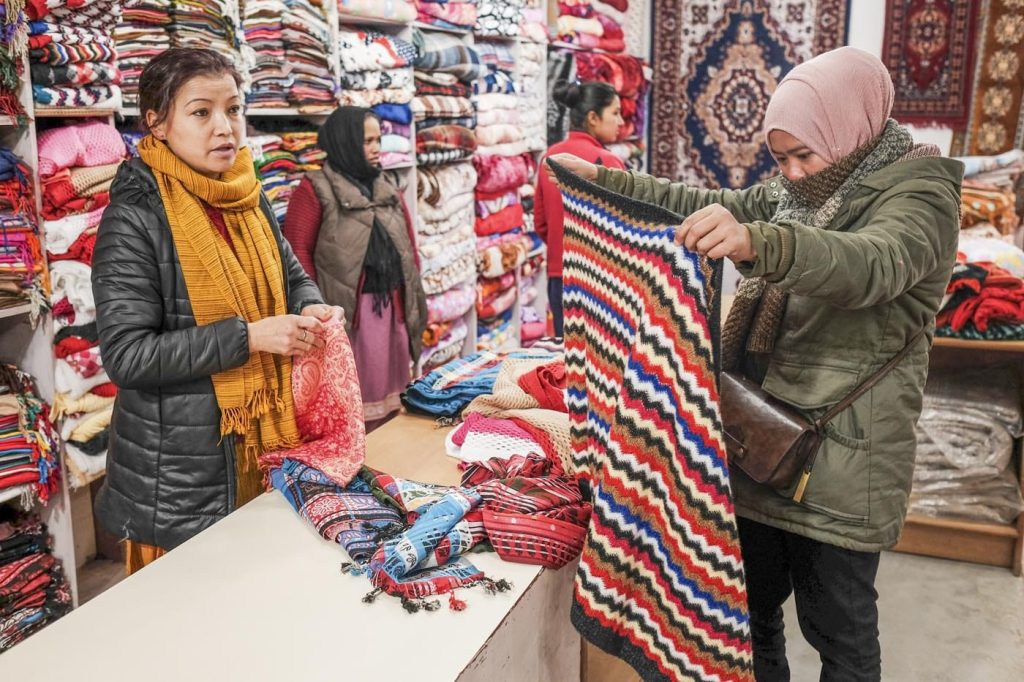
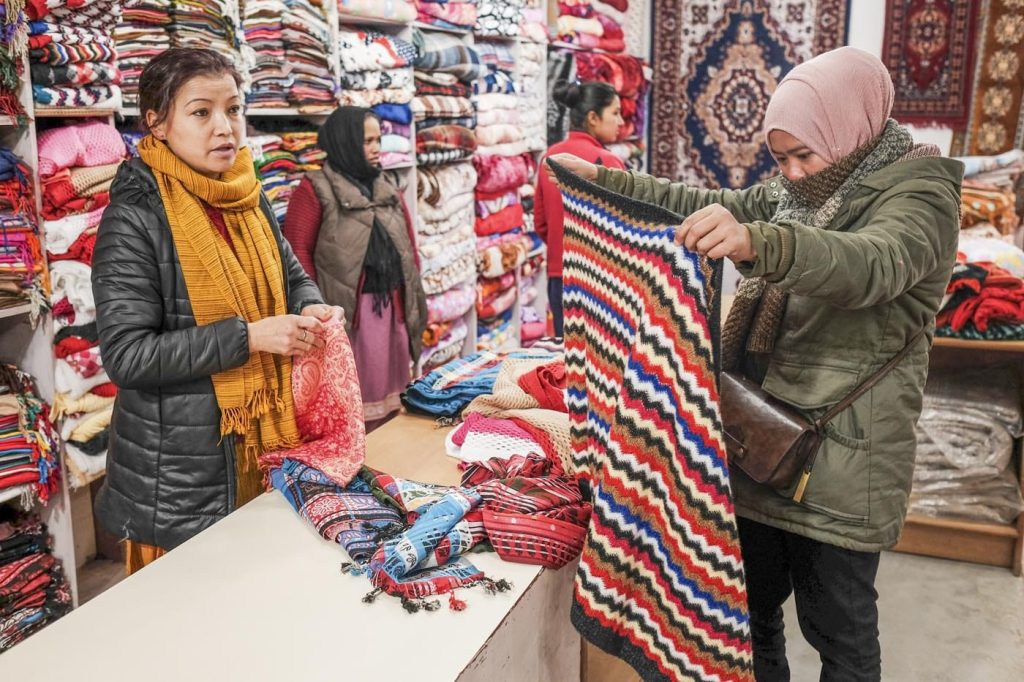
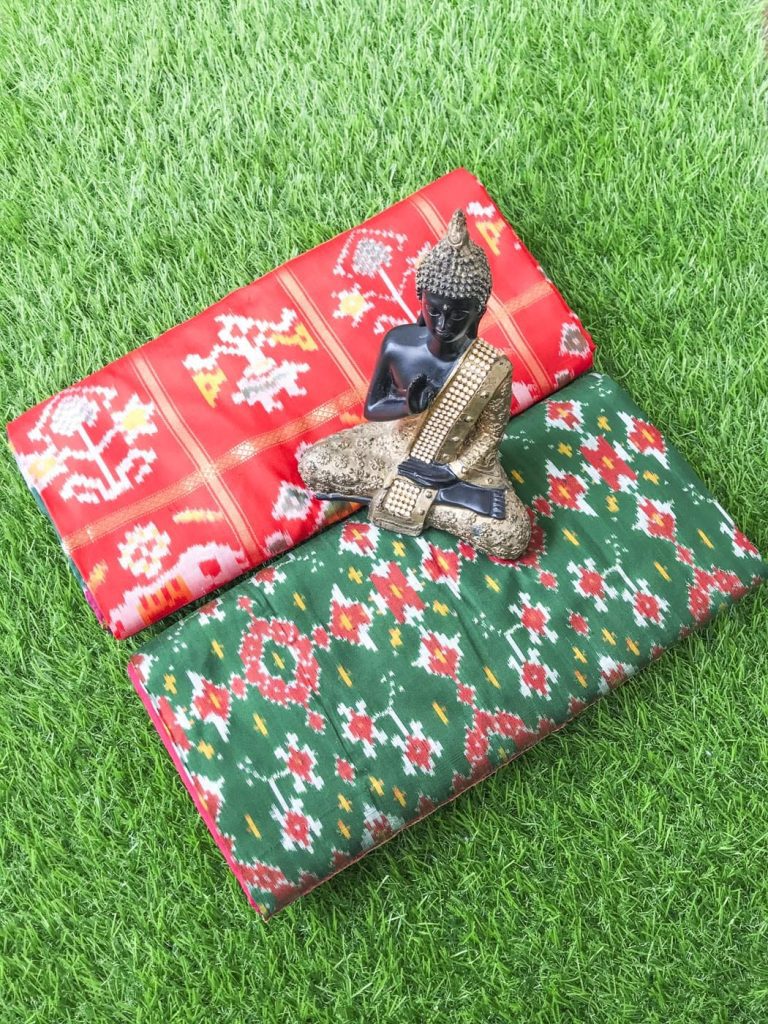
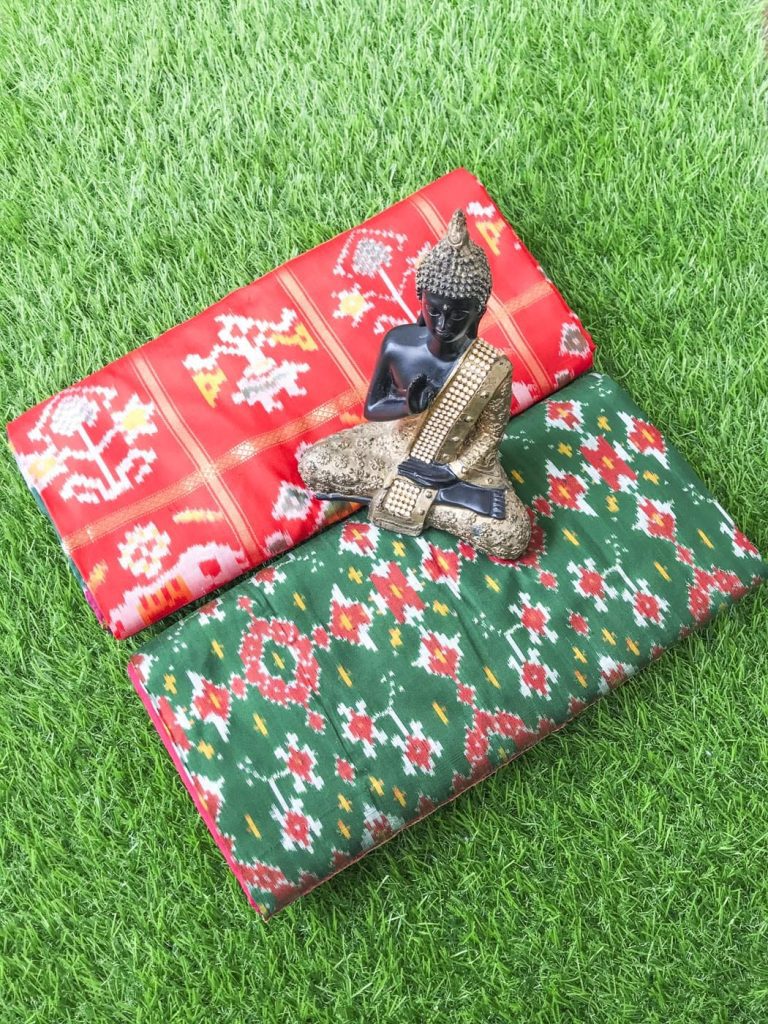
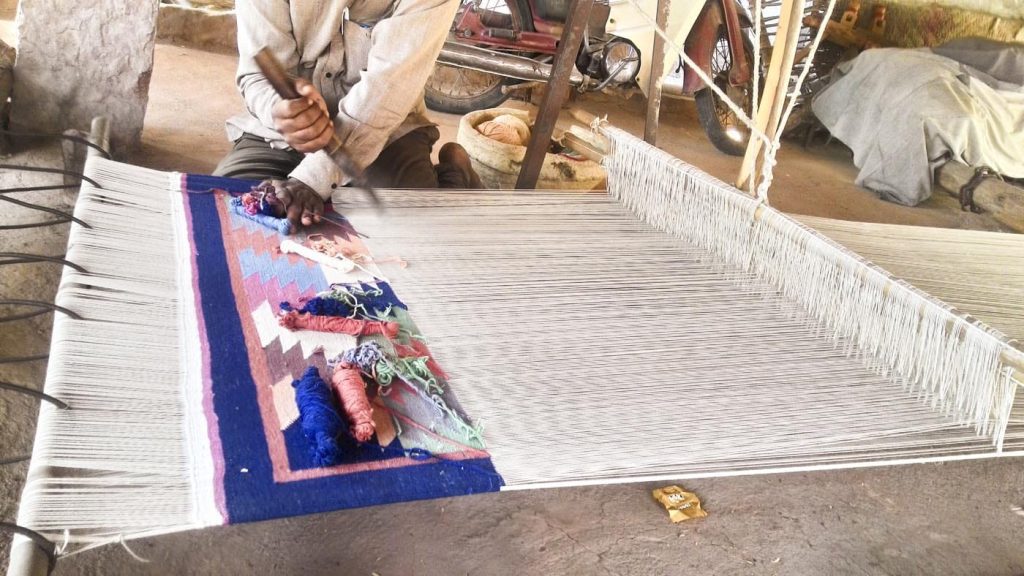
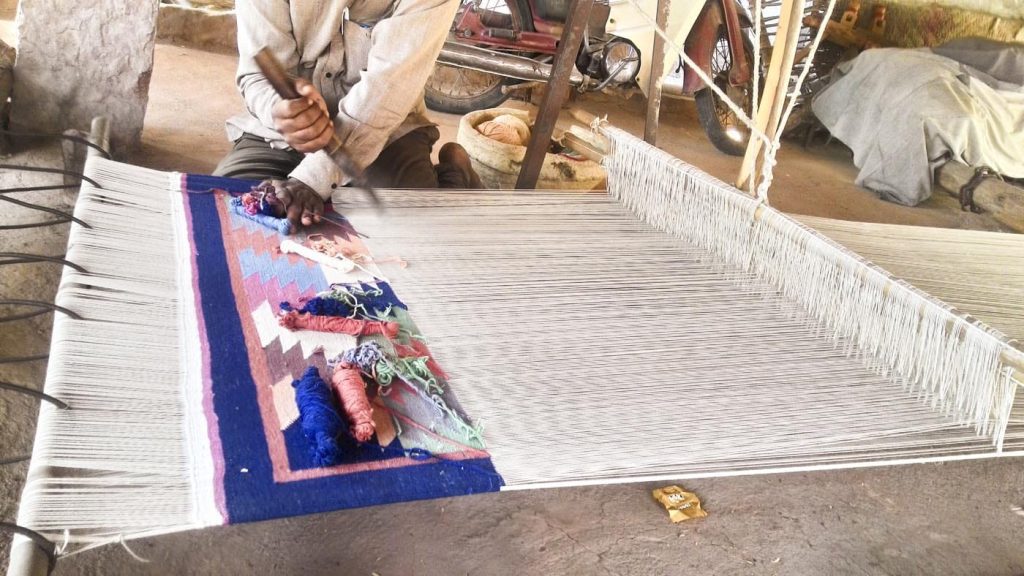
In the tie-dye textile called bandhani,1 originating in the Indus Valley Civilization, the fabric is decorated by tying hundreds of small knots in the cloth, making tiny bindings that form a figurative design. In fact, the word bandhani originates from the Sanskrit word banda that means knot. It is a colorful textile that is created nowadays by the Khatri community from Gujarat.
The traditional kalamkari2pictorial art fabric originated in Andhra Pradesh, where it was used by groups of musicians who moved from village to village recounting some of the most fascinating Hindu myths to local populations. The name kalamkari comes from the Persian word oalam (pen) and kari (craft), but nowadays the kalamkari is known as a manual impression made with stamps or wooden blocks.
The apatani3 weaving technique comes from the Apatani tribe of Arunachal Pradesh. This work can be recognised by its geometrical signs, mostly zigzags and angular shapes.
The kullu4 shawls of Himachal Pradesh are hand woven with three different types of wool: Angora, Merino and wool from local breeds of sheep. Despite their expensive prices, there is a high demand for kullu shawls in India as well as in foreign countries.
Pochampally ikat5 is produced in the town of Bhoodan Pochampally, Telangana region. This weaving is known for its angular signs and the intentional overflow of colors. With about 5,000 hand looms in Pochampally, the village has been elected by UNESCO as one of eight “Iconic Saree Weaving Clusters of India.”
Weaving is not only about textiles, but also carpets. Famous for its tradition of hand looms, the town of Panipat, in the state of Haryana, produces what is called panja durries.6 This technique takes its name from a metallic claw-like tool used to beat and set the threads in the warp. This carpet can be found in almost every house in the state.
In order to produce so many different types of textiles, India boasts more than 23 varieties of cotton. Silk and wool are also produced in a large part of the country, depending on the altitude and climate. Thanks to its huge variety of weaving techniques, India has always been recognized worldwide, and its dominance in this industry has persisted for centuries.
Still today, this hand work, that can definitely be considered an art, remains extremely important to India’s economy, with more than four million people involved. A Ministry of Textiles has been established for the formulation of policy, planning, development, export promotion and regulation of the textile industry in the nation.
In the Modern Context
When weaving is done the traditional way, it is one of the most eco-friendly industries. Hand looms don’t need any external energy. Most looms are located in the textile workers’ houses, in small villages, so minimal transportation is necessary. When raw materials must be carried from place to place, weavers usually use bicycles. Typical looms are 20 to 100 years old and are made of local wood or bamboo. Thus, the ecological impact of this traditional manufacturing is unusually low.


Unfortunately, ecology is often outweighed by the interest of profit and money. Mechanical weaving looms go faster, have a higher productivity and therefore allow for lower prices. China in particular has been a tough competitor for India and is a serious threat to its ancient knowhow, especially because of the massive influx of counterfeit goods.
While a sari made quickly on a mechanical loom sells for around us$100-150, the same sari made on a traditional loom activated by human arms and decorated with human creativity can be sold for the tidy sum of $400. But the hand loom requires many hours of work, and sometimes several days are necessary to create a single sari. The end benefit of a higher sales price doesn’t seem worth the extra effort. Today most young weavers would rather work on electric looms, which are less tiring and arduous than ancient ones.
With education now accessible to most Indian children, the mindset is changing fast. After school, teenagers would rather study, read or play than spend hours weaving next to their parents. Moreover, with access to the Internet and TV, the Western way of life is an aspiration now reachable for most middle-class Indian youngsters. Sitting in front of a loom is not part of their dream anymore. The loss of transmission of the craft is increasing, and some weaving techniques are slowly disappearing. The outfit called puans worn by generations of people from Mizoram state has nearly vanished.
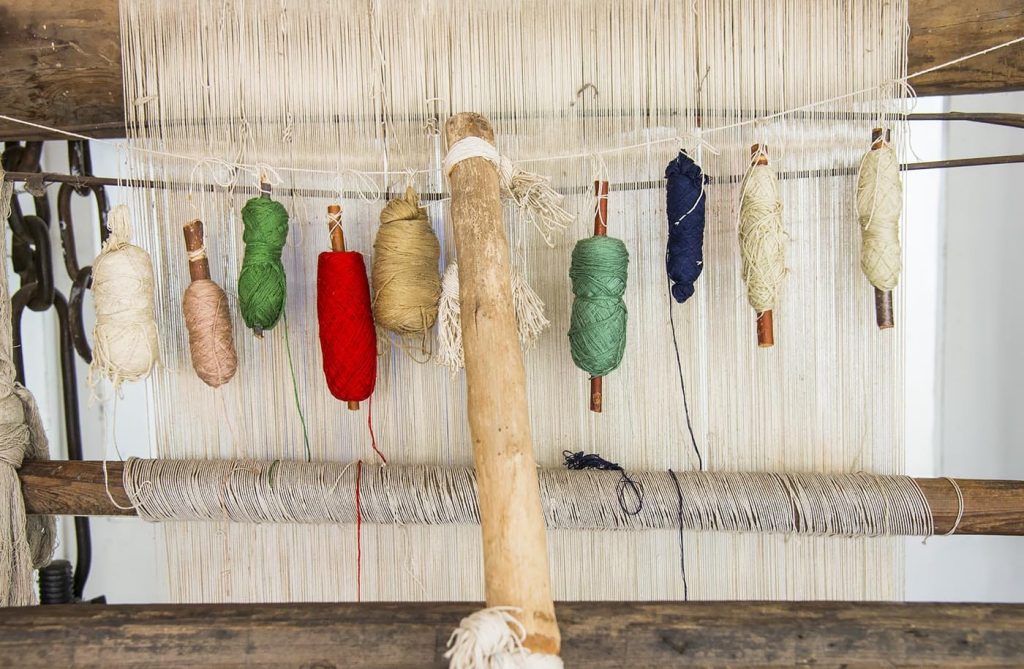
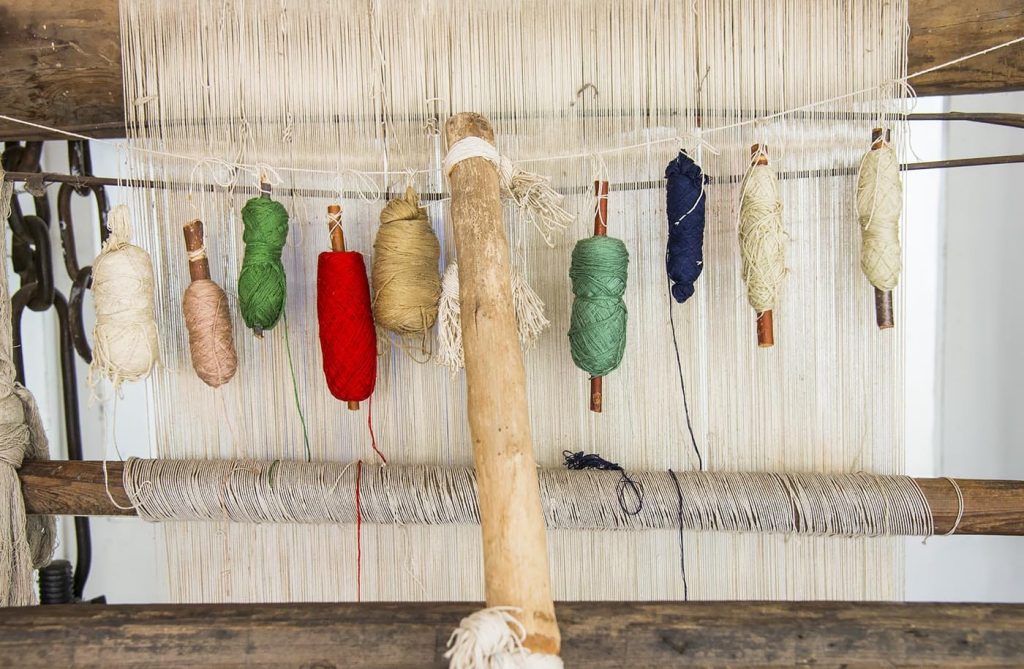
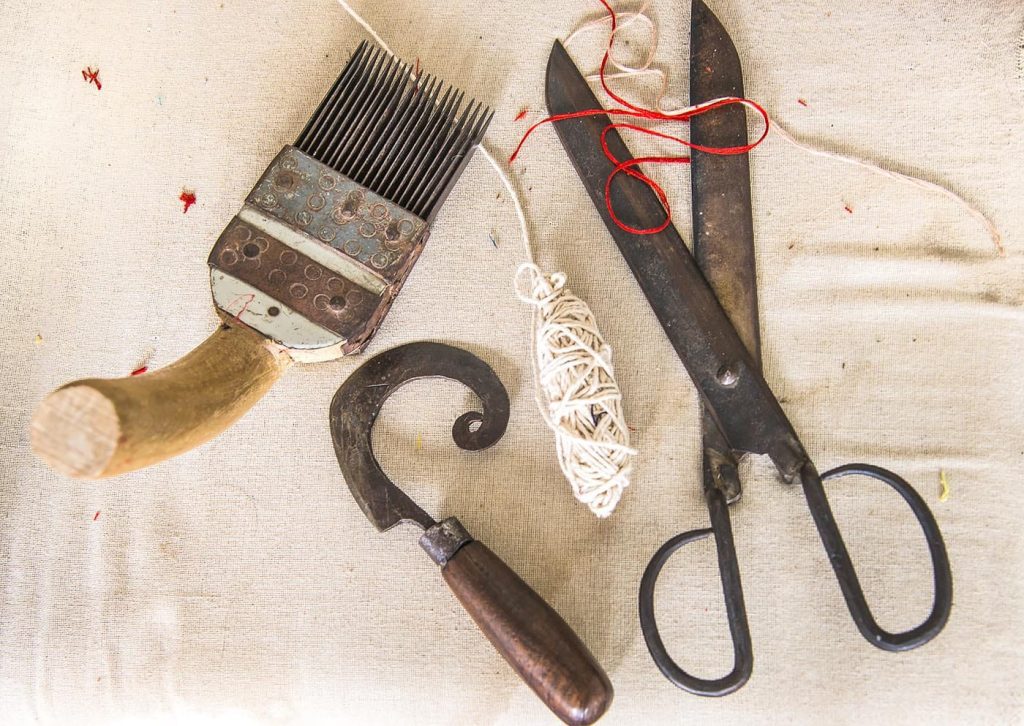
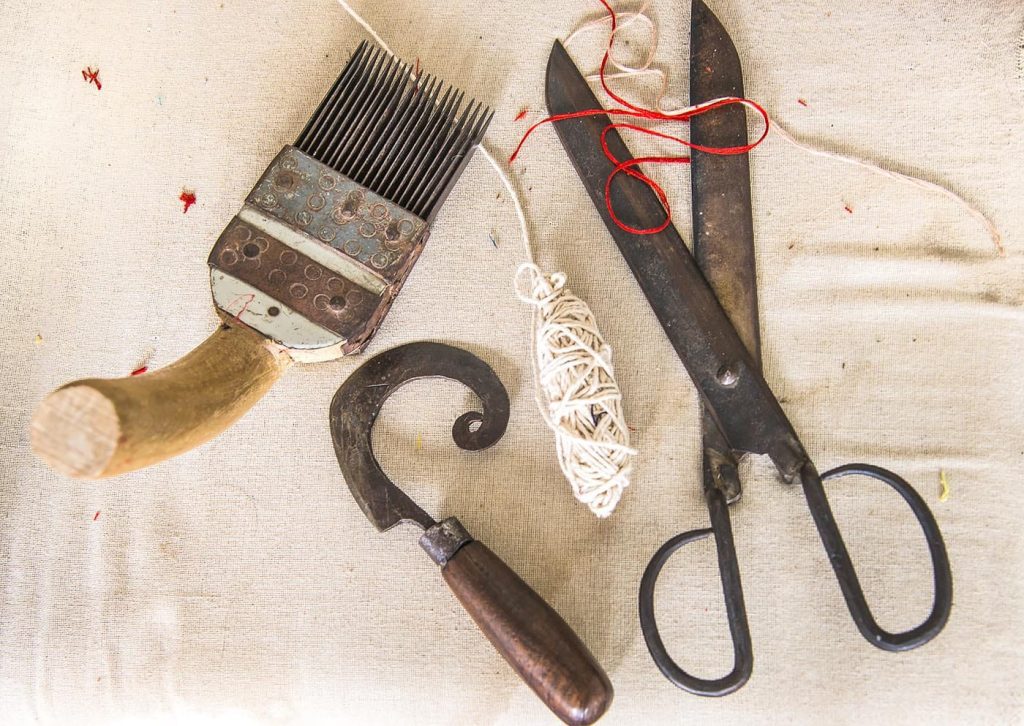
For the last few decades, because of globalization, mechanization and the capacity of some countries to produce huge quantities for very low prices, the Indian weaving industry has endured rough times. But since this sector plays such a vital role of subsistence for a large swath of the Indian population, and as it literally lifts up the economic state of some regions, strong decisions are made. Indians are using their unique intimacy with fabrics, their artisans’ creativity and their ability to adapt traditional designs to modern fashion, to remain on top and to suit various markets in Asia as well as in the rest of the world.
Empowerment for Women
In the past, in many Indian states, children were expected from a young age to help their family by doing all types of work, no matter how hard it was. Their lack of basic education, the impact of the dowry system, and the demands of family life often restricted their opportunities to low-paying, hard physical labor and very difficult lives. This hard labor was especially taxing on girls, while social factors prevented most women from even considering professional training.
Some NGOs are working to change this situation. By providing special weaving coaching and promoting the knowledge some women already have in this field, they support cultural traditions and help women gain extra income for their family through a less demanding occupation. But how to link weavers located in small remote villages with Western clients who have a renewed interest in craft traditions? NGOs located all around India have become a bridge between those local artisans and the rest of the world.
One such organization is Premalaya Handicrafts Trust. This non-profit organization, located in Tiruvannamalai, a largely rural and drought-ridden district of Tamil Nadu, was founded in 1987 to provide village women with training and work in traditional handicrafts, allowing them to improve their family’s economic status. Many women from surrounding villages are participating in the production of crafts with a touch of art in various sectors like embroidery, handloom weaving, handmade cotton dolls, peepal leaf painting, palm leaf weaving, cane furniture, batik and block printing. What began with a day clinic and the training of women health workers has grown into a comprehensive support network for 40 villages. Today, Premalaya handicrafts are designed and created by over 300 women artisans.
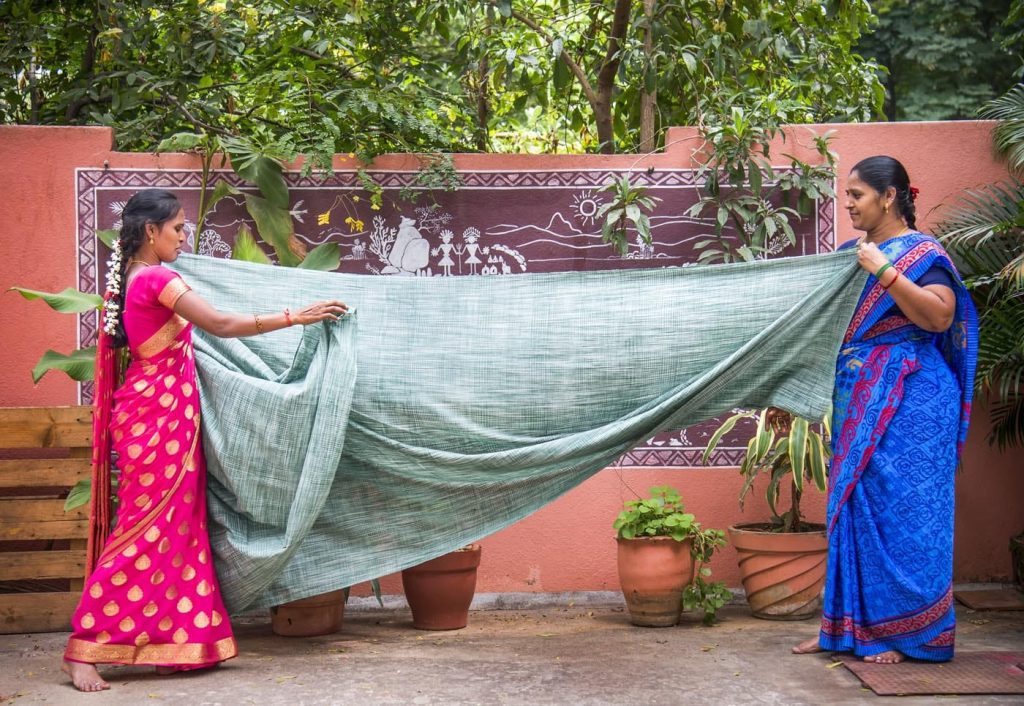
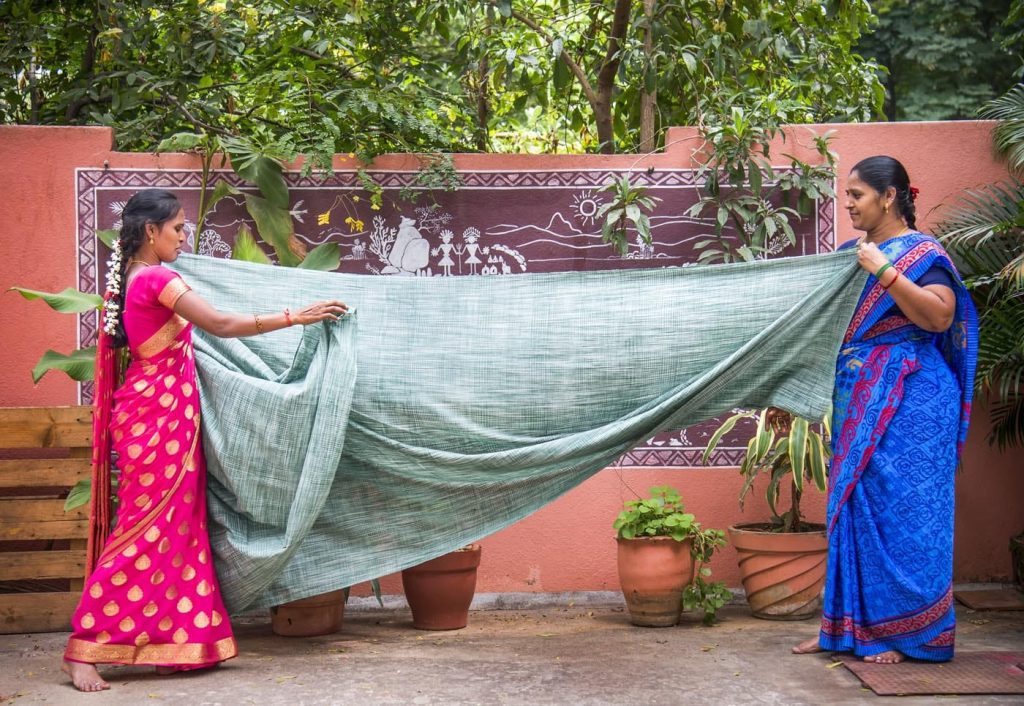
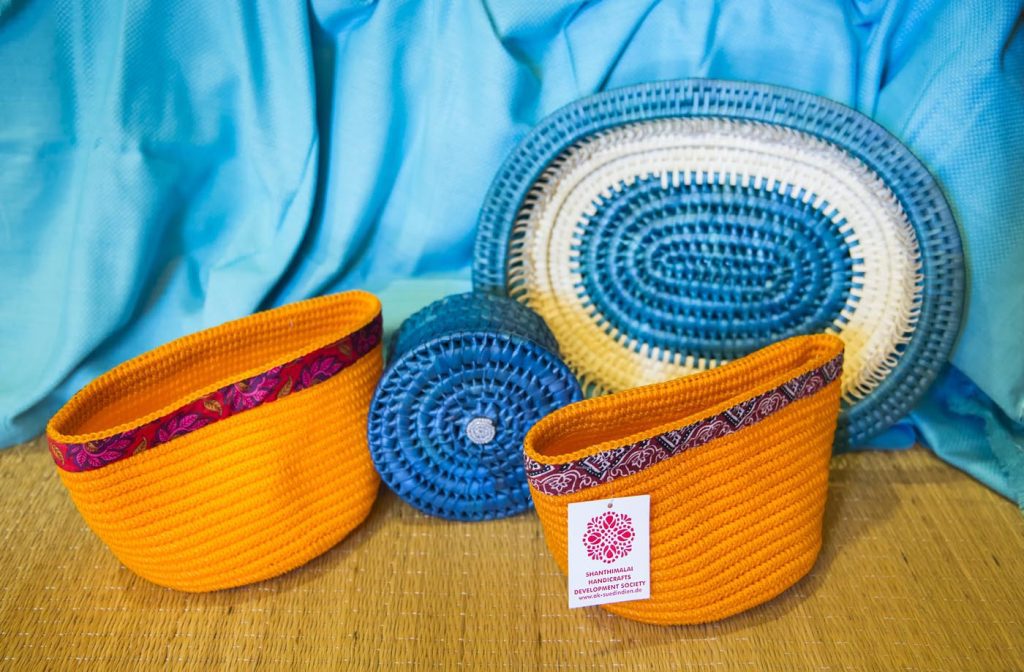
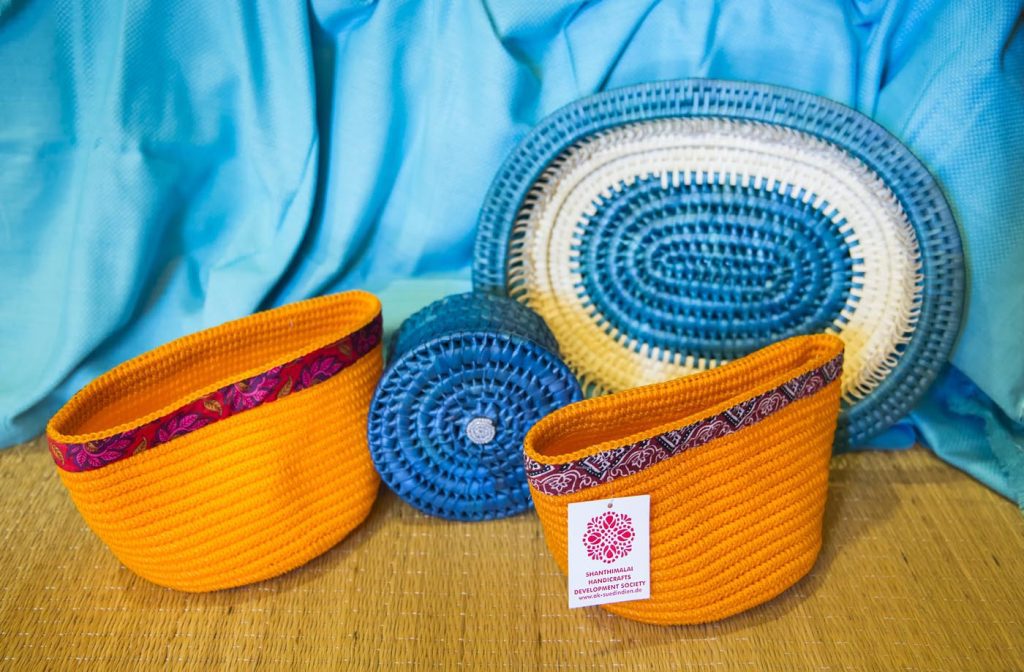
While weaving in the past served to create clothing like saris, shawls or carpets, these days the Premalaya Handicrafts Trust trains women to adapt their work to western demand by producing bags, laptop covers, table mats and cushion covers, following strict international norms of fabrication.
In order to attract more potential clients and western tourists, the NGO has opened a boutique in Tiruvannamalai, selling handmade souvenirs. By supporting an ethical consumerism, this is a win-win deal in every sense: providing work for the local population at a fair salary, giving buyers the opportunity to get original crafts and keeping alive the ancient Indian knowhow of weaving.
Conclusion
Nowadays in just a minute on the Internet we can find all types of objects and clothing, all looking the same and produced by extremely fast and productive machines. However, having a scarf actually made by humans from beginning to end, who took their time to find the best silk possible, who worked hard on handlooms and who used their artistry to create, definitely gives the scarf a special value.
India is betting on the fact that those who value handmade weaving will continue buying traditional crafts. They are not merely buying an object; they are obtaining the artisan’s excellency, their creativity and somehow a little piece of their personal story and national history.